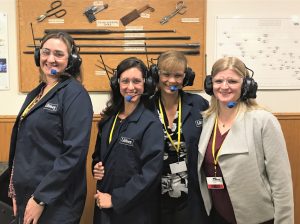
Christina G., Rebecca P., Jennifer V., and Amanda H. preparing for the Libbey plant tour
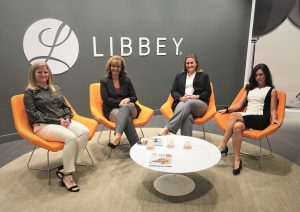
Amanda H., Jennifer V., Christina G., and Rebecca P. lounging at Libbey headquarters
Libbey has been a valued vendor partner of Houston’s for several decades. Our two companies have grown with each other over the years, and formed a unique partnership that we look forward to continuing to build on for many years to come. Members of our management team made a trip to Toledo, Ohio in September to visit Libbey Headquarters and tour one of Libbey’s six manufacturing plants (one of only two located in the U.S.).
The plant tour was an incredibly educational experience during which our team saw the entire glass making process from beginning to end – from raw materials to packaged glass products ready for shipment. “The factory tour was impressive to say the least,” says Amanda Hackathorn, Purchasing Manager. “The plant was huge. but still ran smoothly and efficiently.”
Despite Libbey’s advancements in automation, there are still a few manual processes along the production line. While the stems of all one-and-two piece glasses are pulled via automated processes, Libbey’s signature “Z-stem” is carefully hand twisted using special tong while the glass is still hot malleable.
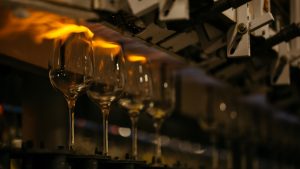
Image courtesy of Libbey
The raw materials are combined and melted together at 2800-degrees Fahrenheit. The glass is pushed though custom-manufactured machinery that portions the molten glass before it is blown in molds, and then slowly cooled in what looks like a large pizza oven for an extended period of time. This process is known as annealing and relieves any residual internal stresses in the glass that commonly occur during manufacturing. Relieving these stresses allows Libbey to better control how the glass breaks. Rather than shattering into lots of sharp, tiny pieces, annealed glass will break into larger pieces with fewer sharp edges. This is key in foodservice where glass commonly breaks and can potentially get into food.
The Toledo factory produces primarily clear and cobalt-colored glass products. While colored glass can be checked for quality assurance purposes via camera, clear glass products are hand-checked for quality because they cannot be “seen” by the camera. Both clear and cobalt items that do not meet Libbey’s strict quality standards are recycled back into future product runs. Small product runs are manually boxed and palletized while palletization for large runs is automated. As you walk through the plant, it’s not uncommon to have conveyor belts carrying product over your head.
While in Toledo, our team had the opportunity to meet with Libbey’s new executive and upper management team members to discuss business challenges, opportunities, and successes as well as strategies for the future that will allow our two companies to continue to grow and support each other. “The Libbey visit was a great opportunity to discuss ways to grow our business with one of our most established and valued vendor partners,” said Jennfer Vigil, President of Houston’s. “The hospitality [Libbey] extended and ability to view their company from both their corporate and manufacturing segments was truly appreciated.”
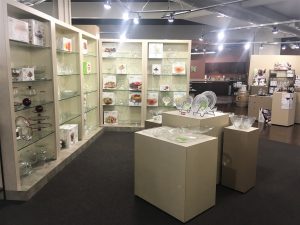
Libbey’s showroom
Libbey’s journey to becoming “america’s glassmaker” began in 1818 in East Cambridge, Massachusetts as New England Glass Company. When Edward Drummond Libbey took over in 1888, he moved the factory to Toledo, Ohio. In 1893, Libbey became a household name when it displayed its beautiful cut glass at the World’s Fair in Chicago. Together with Michael Owens (founder of Owens Corning), Libbey revolutionized the industry when they introduced automation to the glass-making process.
Today, Libbey sells over 1 billion pieces of glass around the world each year. Known for its value, craftsmanship, durability, and innovative designs Libbey is the top producer of casual glass drinkware in the western hemisphere.