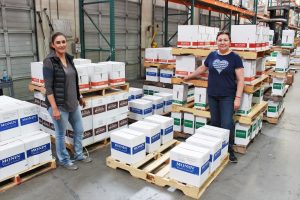
Warehouse Receiving
The flow of material for any warehouse begins with Receiving. What sets Houston’s Receiving Department apart from similar warehouses is that not only do we schedule regular daily deliveries, but we also have the flexibility to accept unscheduled deliveries.
Product delivered is a combination of goods for resale, samples and internal usage. Purchase Orders (PO’s) can be thousands of mixed items or full truckloads of a single item.
Methods for delivering the product are just as varied as the product itself:
- Parcel – Packages received via FedEx or UPS.
- Less Than Truck Load (LTL) – Only part of the shipment is being delivered to Houston’s. LTL can range from 1 pallet to 22 pallets from various shippers per delivery.
- Full Truck Load (FTL) – The entire truck load is dedicated to Houston’s.
- HTrans – Houston’s utilizes its own trucking company to back haul freight to the warehouse.
- Intermodal – This is the transportation of freight in a container using multiple modes of transportation (rail, ship and truck). Shipping intermodal allows product to move around the clock.
Once the product hits the dock, Houston’s simplified and automated process ensures that product is received quickly. Virtually any item can be received, stocked, and on a customer’s order the same day. Houston’s failsafe against lost product on the dock is to consider product received only when it is physically in the pick slot.
Mike Buddrius, Director of Warehouse Operations, is constantly looking for ways to streamline processes. He foresees that in the future Houston’s will be broadening the use of Print on Demand and incorporating voice technology.
Even with added technology product doesn’t receive itself. Mike both compliments and acknowledges their hard work, “Houston’s Receiving crews are knowledgeable, skilled, self-motivated and require very little direction. The Wilsonville location has employees that have been with the company for 10+ years.”
In our Wilsonville location, Receiving Supervisor Brenda Hart remembers using handwritten tags and data entry into the system before product was available for customers. Once inventory technology became available, it sped up the receiving process and product was available almost immediately.
“One thing that stands out with the Receiving crew in Oregon are the years of experience on the team,” notes Brenda. “We have employees with 17 years to [just] 7 years with the company. They have knowledge of the products and the vendors. You can also see the pride they put into their work. We have been putting in some long hours yet everyone continues to have a positive attitude.”
Recently a driver with a trucking company commented to Brenda that, “He was impressed with how nice and helpful everyone was on the receiving dock. It was his third week with the company and he said it was the best place he had delivered to so far.”
While the Kansas City crew has less time on the dock, Day Shift Supervisor Sherman Dodd notes, “The crew is more than Receiving, we wear many hats during the day. Most are fairly new and they’ve done a great job learning the receiving process. They have meshed together well. I’m pretty proud of them.”
This has been an incredibly busy season for the Receiving crews and they are putting in the hours to prove it. Houston’s thanks you for the dedication and hard work!